烧钱和中国抢未来,德国豪赌这个行业
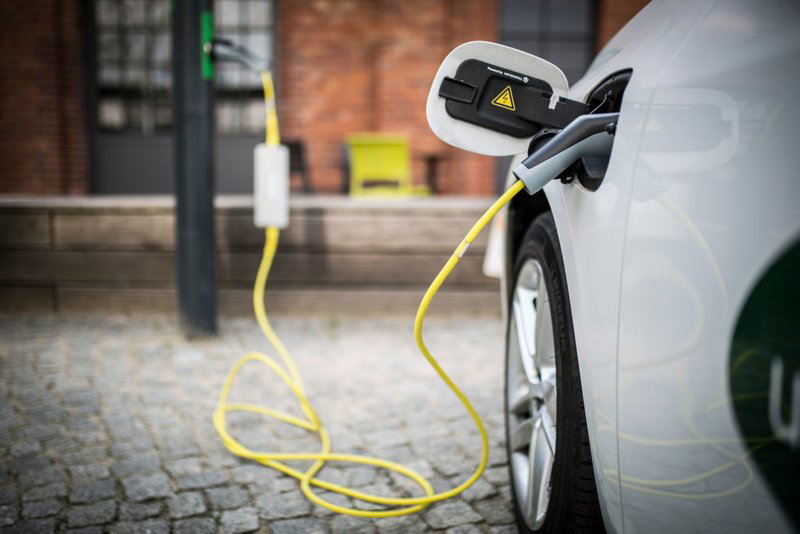
德国政府押宝电池行业,把它作为国家工业未来发展的关键产业。汽车行业对德国经济至关重要,而汽车正在转向电气化。所以,按照这个思路,欧洲——特别是德国——应该制造更多的电动汽车电池。 这当然是一个蓬勃发展的行业。电动汽车电池的销售额预计将于2030年达到600亿美元。但电池制造商绝大多数来自于亚洲,大多又是中国公司,例如宁德时代新能源科技有限公司和比亚迪。它们的崛起得益于中国政府对该国电动汽车制造商的补贴,它们可能会在几年内占据70%的市场份额。市场上还有来自于日本和韩国的大玩家,比如松下(特斯拉和丰田的电池合作伙伴)、LG化工(LG Chem)和三星SDI(Samsung SDI)。 其实德国也想这么干。2018年11月,德国政府宣布向该国公司提供10亿欧元(11.2亿美元)的基金,用于开发生产电池。德国在今年2月公布的《2030年国家工业战略》(National Industrial Strategy 2030)则显示出了焦虑,表示“如果未来人工智能自动驾驶的数字平台来自于美国,未来汽车的电池来自于亚洲,德国和欧洲将在该领域损失超过50%的附加值。”解决方案是什么?国家对电池生产提供支持。 说的委婉些,并非每个人都认为这是一种合理的办法。“这是在烧纳税人的钱。”杜伊斯堡-埃森大学的汽车经济学教授、曾经在欧宝和保时捷等公司任职的行业资深人士费迪南德·杜登霍夫说,“这么干很蠢,经济部的所作所为太疯狂了。” 按照杜登霍夫的说法,政府找错了方向,因为利润其实来自于主要的电池组件:阴极和阳极。“电池的产值约为15%。阴极材料占60%,阳极材料占20%。”他说,“他们准备投资10亿欧元用于电池生产,但这个过程不产生价值。价值来自于材料。” 追赶中的困难 德国的巴斯夫(BASF)是世界上最大的化学公司之一,当前的工作中心就是生产电池材料,它正在与俄罗斯的矿业公司Nornickel合作,在芬兰建立阴极材料工厂。但是,公司的一位发言人表示,巴斯夫还认为“在欧洲国家进行更大规模的电池生产投资十分重要,这样可以确保电池材料具有足够的供应,提高竞争力,这样欧洲就毋需完全依赖进口电池供应。” 还有很多德国公司——包括像大众这样的汽车制造商——也许听进去了丰田执行副总裁寺师茂树的意见,“征服电池的人将征服汽车电气化”,都在认真考虑生产自己的电池。 试图赶上亚洲电池制造商的最大问题是,该行业起步时需要大量投资,但是这个生产过程一旦开始运行,后续重复建设的成本则相对较低。 正如杜登霍夫所言,世界上最大的电动汽车电池制造商、中国的宁德时代在华拥有三家工厂,目前正在德国的埃尔福特市投入约2.4亿欧元建造一座生产电池的“超级工厂”。德国的工程巨头博世公司几年前也考虑建一座电池工厂,估计耗资200亿欧元。博世在去年放弃了该计划,称投资规模太大,风险过高。 新兴技术研究机构IDTechEx的首席能量存储分析师何晓溪同样认为,对想要生产电动汽车电池的德国汽车制造商和其他公司来说,至少短期内“经济上的投入产出并不合理”。不过,她补充道,这个行业存在很多变量,比如说公司的规模和经济实力很重要,与亚洲电池公司的关系也同样重要。 欧洲“制衡” 如果有公司想表示对德国政府10亿欧元的电池基金有兴趣,3月中旬是最后期限,申请者可以等到复活节把提案扩充为成熟的申请方案。目前总共提出了大约30个项目,申请者包括汽车制造商,也有零配件、材料和化学品制造公司。 申请者总部必须设在德国,但该援助计划的最终目的是拓展至整个欧洲,项目将涉及与其他欧盟国家的协调,这些国家也在向德国公司提供资金。 在资金分配的过程中,申请者的详细信息将保密,但有些公司已经自行发布了公告。汽车制造商包括大众和宝马,大众希望为研发和“产业化实施”得到资助,而宝马公司将把现金用于研发,该公司已经签约成为宁德时代埃尔福特工厂的第一位电池客户。 大众正在开展规模巨大的电动汽车项目,使用的电池来自于多家亚洲供应商,但公司的首席执行官赫伯特·迪斯在上个月表示,公司“也在密切关注参与欧洲电池制造的可能性。”梅赛德斯的制造商戴姆勒已经开始在德国生产电池,而且正在波兰建电池厂。 |
The German government has placed a big bet on batteries as a key to the country’s industrial future. The automotive industry is vital to the German economy, and cars are going electric. So, the thinking goes, Europe—and Germany in particular—should be making more electric car batteries. It’s certainly a booming industry; electric car battery sales are projected to hit $60 billion by 2030. But the companies making the batteries are overwhelmingly Asian. Most are Chinese firms such as Contemporary Amperex Technology Co. Limited (CATL) and Build Your Dreams (BYD), whose rise was fostered by state subsidies for Chinese electric carmakers and which are likely to hold 70% of the market in a couple years’ time. There are also big Japanese and South Korean players such as Panasonic (Tesla and Toyota’s battery partner,) LG Chem and Samsung SDI. Germany wants some of that action. Last November, the government announced a €1 billion ($1.12 billion) fund for German companies to develop and build battery cells. Germany’s “National Industrial Strategy 2030,” unveiled in February, fretted that “if the digital platform for autonomous driving with Artificial Intelligence were to come from the USA and the battery from Asia for the cars of the future, Germany and Europe would lose over 50% of value added in this area.” The solution? State assistance for battery cell production. But not everyone is convinced this approach makes sense, to put it mildly. “It’s burning taxpayers’ money,” said Ferdinand Dudenhöffer, professor of automotive economics at the University of Duisberg-Essen and a veteran of car firms such as Opel and Porsche. “It’s stupid. It’s crazy, what our ministry of economics is doing.” According to Dudenhöffer, the government is looking for value in the wrong place, as the money is really in the main battery components: cathodes and anodes. “The production value of the cell is about 15%. Sixty percent is just in the materials of cathode, and another 20% is the materials of anodes,” he said. “The value does not exist in the manufacturing process in which they want to spend €1 billion. The value is in the materials.” Catch-up challenges Germany’s BASF, one of the world’s biggest chemical companies, is focusing on battery materials—it’s building a cathode materials factory in Finland, in cooperation with Russian miner Nornickel. But, a company spokesperson said, BASF also believes it is “crucial to invest on a much larger scale in cell production in European countries and thus ensure reliable supply of battery materials and competitiveness, so that Europe will not be solely dependent on imported cell supplies.” And there are plenty of German companies, including carmakers such as Volkswagen—perhaps heeding the assertion of Toyota executive vice president Shigeki Terashi that “the one who conquers batteries will conquer the electrification of cars”—that are seriously looking at producing batteries themselves. The biggest problem with trying to play catch-up with the Asian battery manufacturers is that it takes a lot of investment to get started with the manufacturing process, but, once you’re up-and-running, replicating that process is relatively cheap. As Dudenhöffer noted, China’s CATL—the world’s biggest electric vehicle battery manufacturer with three factories back home—is building a “gigafactory” battery plant in the German city of Erfurt for around €240 million. When the German engineering giant Bosch was considering building a battery plant a couple years back, it estimated a cost of €20 billion. Bosch dropped those plans last year, saying the size of the investment made the plan too risky. Xiaoxi He, lead energy storage analyst at emerging technologies research outfit IDTechEx, agreed that “financially it does not really make sense” for German automakers and other companies to try producing electric car batteries in Germany, at least in the short term. However, she added, there are a lot of variables that could change the business case—size and financial strength matter, for example, as do relationships with Asian battery companies. A European ‘counterweight’ The deadline for companies to express interest in the German government’s €1 billion battery pot was in mid-March, and the applicants have until Easter to flesh out their proposals into full-blown applications. All in all, there have been around 30 projects proposed, with prospective applicants including everyone from automakers to parts, materials, and chemicals firms. Applicants have to be based in Germany, but the state aid initiative is ultimately intended to be European in nature, involving coordination with other EU countries that are also offering cash to their companies. Details of the applicants remain confidential while the allocation process is ongoing, but some have made their own announcements. As automakers are concerned, they include Volkswagen, which wants funding for both R&D and “industrial implementation,” and BMW, which will steer the cash toward research and development: it’s already signed up as the first customer for the batteries coming from CATL’s Erfurt plant. VW is currently using a variety of Asian battery suppliers for its enormous electric-car push, but CEO Herbert Diess said last month that the company “is also taking a close look at possible participation in battery cell manufacturing facilities in Europe.” Mercedes-maker Daimler is already making some batteries in Germany, and is building a battery plant in Poland too. |
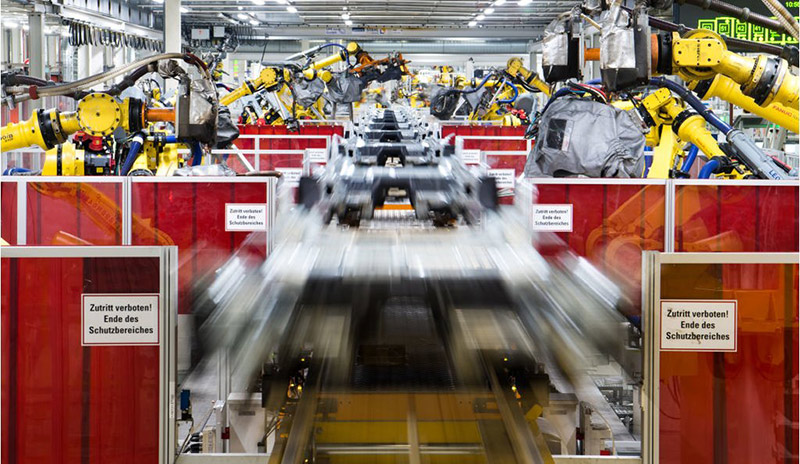
按照德国经济部的说法,帮助欧洲公司“制衡”已有的亚洲供应商是非常重要的。 “未来电力存储单元将用于许多不同的产品(自行车、汽车甚至飞机),对电池的需求将与生产能力同步增长。这将关系到未来大量的工作岗位、价值链和专业知识。”经济部的一位发言人表示,“因此,我们德国和欧洲需要具有竞争力、创新及环保的电池制造能力。” “已经有许多家感兴趣的公司根据我部发出的邀请申请资金。”发言人说,“申请额度已经超过可用金额数倍,说明行业对推动这项工作十分感兴趣。” 未来的技术 对于一些争夺政府资金的公司而言,“推动”意味着将目前的液态锂离子电池技术推向可能需要几年发展时间的新技术:固态电动汽车电池。 业界希望固态电池能够提供更大的能量密度,拥有更大的电池容量、更长的行驶里程。它们还应该比液态锂离子电池充电更快,并且不易着火。 “我们认为液态锂离子技术的潜力无法完全满足市场对于行驶里程、重量和成本的要求,因此我们认为我们需要跨越至另外一种技术,这种技术可能是固态电池。”德国汽车零部件供应商大陆集团(Continental)的发言人表示,该公司希望使用部分政府资金用于研发。“现在进入液态锂离子市场已经太晚了。投资太高,而且我们看不到未来的潜力。” 大陆集团表示将在明年决定是否继续推进固态电池的生产。然而,哪怕这种商业模式看起来有足够的吸引力,该公司最早也要到2025年才能够建立起充足的产能,实现规模化生产。该公司的发言人表示,即使到那时,出于对工厂成本的考虑,东欧国家“当然比德国更有潜力”。 杜登霍夫教授认为,固态电池需要十年或更长时间才能实现产业化。“在接下来的五年里,没有人真的会期待实现技术突破,彻底淘汰液态电池。”他说。巴斯夫也表示,预计“在可预见的未来,锂离子电池仍将继续是电动汽车的主流技术”。 与此同时,杜登霍夫建议,欧洲公司应该先把生产抛诸脑后,专注于研究可以克服寒冷天气耗电快等问题的材料。 “在我来看,或许宝马[的方法最好],因为他们只是想了解电池中的化学成分。”杜登霍夫说道,“他们想找出哪种是最好的电池,最好的性能是什么,然后去问他们的供应商:‘我想要那个电池,价格是多少?’”(财富中文网) 译者:Agatha |
According to Germany’s economics ministry, there really is a point to helping European companies “form a counterweight” to the established Asian suppliers. “Electricity storage units will be used in many different applications in future (bicycles, cars, even aircraft), and demand for batteries will rise in parallel to the production capacities. This will involve a large amount of jobs, value chains and expertise for the future,” said a ministry spokesperson. “We in Germany and Europe therefore need competitive, innovative and environmentally friendly battery cell manufacturing capacities.” “Numerous interested companies have applied for funding in response to the invitation issued by the Ministry,” the spokesperson said. “The amount available is oversubscribed several times over, suggesting that industry is extremely interested in moving forward on this.” Future technology For some of the firms vying for government funding, “moving forward” means looking beyond today’s liquid lithium-ion battery technology to a development that could be some years away: solid-state electric car batteries. The industry hopes that solid-state batteries will provide greater energy density, and therefore greater capacity and driving range. They should also charge more quickly than liquid lithium-ion batteries, and be less prone to catching fire. “We think that liquid lithium-ion technology does not have the potential to fully fulfill the demands we see from the market regarding range, weight and cost, so we think we need to have a leap to another technology that could be solid-state,” said a spokesperson for the German automotive parts supplier Continental, which wants to use some of that government cash to fund R&D. “It’s too late to go into the liquid lithium-ion market. The investment would be too high and we do not see the future potential.” Continental says it will decide next year whether it wants to press ahead with the production of solid-state batteries. However, even if the business model looks sufficiently attractive, it would take the company until 2025 at the earliest to build up its capacity and go into mass production—and even then, the firm’s spokesperson said, plant cost considerations mean Eastern European countries are “of course more promising” than Germany. As far as Professor Dudenhöffer is concerned, it will take a decade or more for solid-state batteries to become an industrial reality. “In the next five years, nobody is seriously expecting a breakthrough technology which will make liquid obsolete,” he said. BASF, too, said it expects that “lithium-ion batteries will remain the prevailing technology in electric vehicles for the foreseeable future.” In the meantime, Dudenhöffer suggested, European companies should forget about production and focus on researching battery materials that can overcome problems, such as the tendency of cold weather to drain batteries more quickly. “From my point of view, BMW [has the best approach] because what they want to do is just to understand the chemistry in the cell,” Dudenhöffer said. “They want to find out which is the best cell, what is the best performance, and go to their supplier and say, ‘I want to have that cell, what is the price?'” |